
PVD-Beschichtungen: Wie und warum
Das Akronym PVD steht für Physical Vapor Deposition und bezeichnet eine Reihe von Techniken zur Abscheidung dünner Schichten.
FFDiese Methoden werden seit den späten 1960er-Jahren weithin eingesetzt, um Materialschichten für Forschung und Industrie zu herzustellen, die von Elektronik bis Mechanik, vom Bau bis zur Mode reichen, da sie eine präzise Abstimmung der Zusammensetzung und Dicke der Schichten ermöglichen und so Systeme mit speziellen und kontrollierten Eigenschaften entstehen lassen.
Am Markt sind innovative Produkte von höchster Qualität gefragt, weshalb PVD im Bereich der industriellen Beschichtungen immer mehr an Bedeutung gewinnt. Die Verbreitung der Technologie wird jedoch vor allem in Italien durch das mangelnde Bewusstsein und die Tatsache eingeschränkt, dass sie trotz ihrer jahrzehntelangen Geschichte als neu wahrgenommen wird.
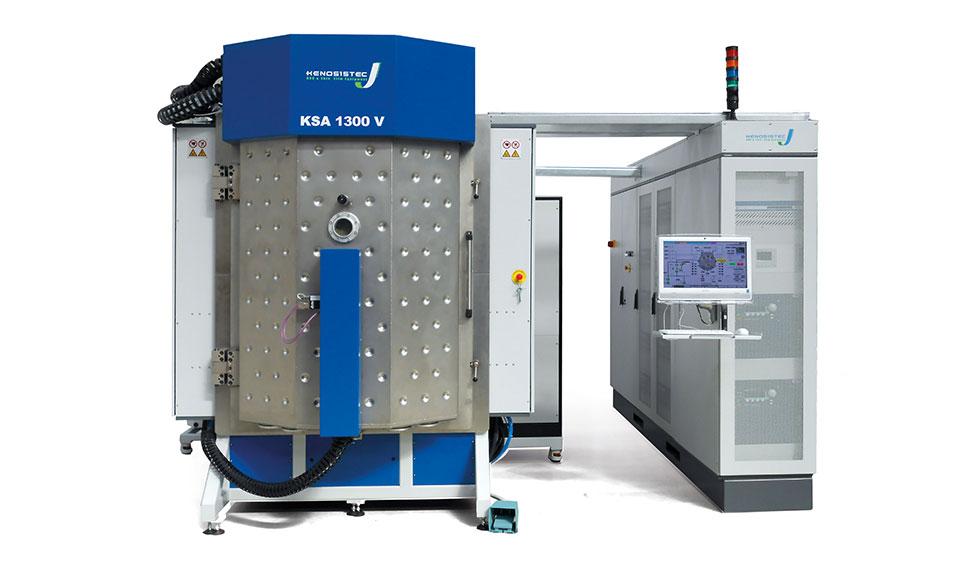
PVD-Technologie in Kürze
Bei der PVD-Abscheidung wird ein Material (das Target) in die Dampfphase gebracht, so dass es an die Oberfläche des zu beschichtenden Objekts (des Substrats) gelangen kann, wo es unter Bildung des sogenannten Films kondensiert. Dieser atomare Abscheidungsmechanismus ermöglicht neben der Verbesserung der Haftung des Films die Verwendung einer breiten Palette von Materialien zur Beschichtung von Substraten verschiedener Art, von Stahl bis Messing, von Eisen bis Zamak, aber auch von Kunststoffen, Glas und Keramik, im Gegensatz zu anderen Technologien, die auf wenige Arten von Metallen beschränkt sind.
Sputtern, Kathodenlichtbogen und thermisches Verdampfen (oft einfach Metallisieren genannt) sind die wichtigsten Methoden auf industrieller Ebene und sie unterscheiden sich darin, wie die Bestandteile (Atome und Ionen) der Dampfphase aus dem Target extrahiert werden und welche Energie ihnen zugeführt wird. Die Entscheidung für eines der Verfahren richtet sich nach den zu erzielenden Eigenschaften hinsichtlich Kompaktheit, Haftung und Farbe des Films sowie nach der Art des abzuscheidenden Materials. Im Einzelnen:
- Sputtern: Das Target wird von einem Regen von Partikeln aus einem ionisierten Gas (Plasma) getroffen. Diese „Kugeln“ erodieren das Material und extrahieren die Atome, die sich dann gleichmäßig auf dem Substrat absetzen.
- Kathodischer Lichtbogen: Eine elektrische Entladung erzeugt eine örtliche Verdampfung am Target, die dann eine Strömung aus ionisiertem Material in Richtung des zu beschichtenden Gegenstands erzeugt. Da es sich dabei um Ionen handelt können sie mit Energie versorgt werden, um kompakte und widerstandsfähige Beschichtungen zu erhalten.
- Thermisches Verdampfen (oder Metallisieren): Das abzuscheidende Material wird in einen Tiegel gegeben und auf eine hohe Temperatur gebracht, die eine schnelle Verdampfung zum Substrat hin bewirkt.
Ein Vakuum ist notwendig, um diese Mechanismen auslösen zu können, sowie um den Transfer des Materials zu begünstigen, das nicht durch Luft oder ein anderes Fluid verlangsamt wird und die Oberfläche des Substrats mit mehr Energie erreicht, wodurch es besser haftet. Obwohl die Erzeugung des Vakuums in der Prozesskammer ein Hindernis zu sein scheint, hat sie in Wirklichkeit zwei grundlegende Vorteile:
- Kontaminationen zu minimieren und somit qualitativ hochwertige Beschichtungen zu erhalten;
- FFEin definierter und wiederholbarer Abscheidungsprozess, wobei das Vakuum ein gut kontrollierter Betriebszustand ist, im Gegensatz zu einer galvanischen Abscheidung, die sehr empfindlich auf Ionenkonzentration und Zusatzstoffe, Stromdichte, Temperatur und Polarisation reagiert.
Schadstoffhaltige Lösungen werden bei PVD-Vorgängen nicht eingesetzt und die verwendeten Metalle sind rein, daher kommt es bei der Abscheidung nicht zu einer Ausbreitung umweltschädlicher Stoffe in die Atmosphäre. Dadurch ist diese Technologie nachhaltig und mit dem steigenden Bewusstsein für ökologische Probleme kompatibel ist.
Eine weitere Stärke der PVD-Technologie ist die Möglichkeit, Verbundwerkstoffe (Nitride, Carbide, Oxide), die aus verschiedenen Elementen bestehen, durch das Einbringen von Gasen herzustellen, die sich mit Atomen verbinden, die sich ablagern. So entstehen Beschichtungen mit besonderen Eigenschaften wie die hohe Verschleiß- und Kratzfestigkeit der Nitride, aber auch Sonderfarben sind möglich, die mit anderen Technologien nicht erzielt werden können. Gerade aus diesen Gründen wird PVD mitunter als ergänzende Technologie zu anderen Behandlungen eingesetzt. Beispielsweise wird in einigen Fällen eine galvanische Vorbeschichtung verwendet, um eine glänzende Oberfläche herzustellen und die Korrosionsbeständigkeit zu erhöhen, wonach eine dünne PVD-Schicht aufgetragen wird, um Härte und den jeweils gewünschten Farbton, von Strohgelb bis Gold, von Chrom bis glänzendem Schwarz, von blassem Rosa bis Kirschbraun zu erhalten.
Die Anlage und die Abscheidung
Eine PVD-Anlage besteht im Wesentlichen aus drei Teilen: der Prozesskammer, dem Pumpsystem und der Steuerelektronik. Die ersten beiden sind eng miteinander verbunden, denn größere Kammern, die entsprechend der Form der zu beschichtenden Gegenstände und der gewünschten Produktivität dimensioniert sind, erfordern Pumpsysteme mit höherer Kapazität. Die Elektronik steuert hingegen alle Komponenten des Systems, reguliert und passt die verschiedenen Parameter so an, dass der Prozess stabil und wiederholbar ist.
Ein Vorgang von grundlegender Bedeutung, der vor der Abscheidung erfolgt, ist mit Sicherheit die Vorbereitung der Stücke. Je nach zu beschichtendem Gegenstand und Materialien (z. B. Zamak, Messing und Kunststoffe), kann eine galvanische Vorbehandlung oder Lackierung erforderlich sein, um eine für chemische Agenzien undurchdringliche glänzende Oberfläche zu erzeugen. Die Reinigung der Gegenstände ist in der Bearbeitungskette unverzichtbar. Sie kann manuell oder mit einem Ultraschallsystemen erfolgen. Sie erfordert besondere Sorgfalt, da beim Arbeiten im Vakuum die Substanzen, die durch Verdampfen das Pumpen der Kammer verlangsamen oder den Prozess verunreinigen könnten, so weit wie möglich eliminiert werden müssen.
Saubere oder vorbehandelte Gegenstände und der Rahmen aus rotierenden Karussellen, die eine gleichmäßige Verteilung des Materials auf einer 3D-Oberfläche erzielen sollen, werden in die Kammer eingesetzt. Nach Erreichen des idealen Vakuums für die Abscheidung werden die Quellen, also die mechanischen und elektronischen Vorrichtungen, die zur Extraktion der Atome des Targets dienen, eingeschaltet. Soll gleichzeitig ein Oxid, Nitrid oder Carbid entstehen, kann ein Sauerstoff, Stickstoff bzw. Kohlenstoff enthaltendes Gas hinzugefügt werden. Durch Variation des Gasstroms und der Extraktionsgeschwindigkeit von Atomen aus dem Target können Materialien unterschiedlicher Zusammensetzung und damit mit unterschiedlichen physikalischen Eigenschaften und Farben hergestellt werden. Je nach Zweck der Beschichtung, dekorativ oder funktionell, wird üblicherweise eine Schicht zwischen 0,2 und 5 µm Material abgeschieden. Dies wirkt sich auf die Dauer des Prozesses aus, die je nach gewünschter Beschichtungsart und angewandter Technik von einigen bis zu mehreren zehn Minuten reicht. Danach wird die Luft wieder in die Kammer eingebracht und die Gegenstände können entnommen werden, ohne dass weitere Behandlungen erforderlich sind. Auch sind keine Entsorgungsvorgänge notwendig, da mit dieser umweltfreundlichen Technologie kein Abfall anfällt.
Der scheinbar komplizierte PVD-Prozess wird vollständig von der Software gesteuert, die automatisch Gasflüsse, Pumpen, Zeiten, Spannungen und die Rotation des Werkstücks regelt und alle Teile des Rezepts steuert, also die Reihenfolge der Vorgänge, die zum Endergebnis führen. Durch die Strukturierung moderner Systeme bereitet die PVD-Technologie keine größeren Anwendungsschwierigkeiten als andere Technologien wie z.B. galvanische Abscheidung oder Lackierung.
Wie jede industrielle Maschine erfordern auch PVD-Maschinen Wartungsvorgänge, von der regelmäßigen Reinigung der Kammer bis zum Austausch der Targets. Diese Vorgänge werden durch eine intelligente Systemauslegung vereinfacht. Es liegt in der Verantwortung des Herstellers, ein effizientes, zugängliches und intuitiv verwendbares System in bereitzustellen, das den Bedürfnissen des Kunden entspricht.
Eine PVD-Anlage ist ein technologisch fortschrittlicher und raffinierter Gegenstand, wodurch die höheren Kosten gerechtfertigt werden. Im Gegenzug garantiert sie Zuverlässigkeit und Vielseitigkeit. Mit diesen Eigenschaften können Produkte von ästhetischem und technischem Wert hergestellt werden, die jenen Produkten überlegen sind, die mit traditionelleren Techniken hergestellt werden. Vor allem entsprechen die Produkte stets den Trends und Anforderungen am Markt. Darüber hinaus können dank der zahlreichen Möglichkeiten, die PVD bietet, neue Produktlinien für noch nicht durchdrungene Märkte entstehen.
Anwendungsgebiete
PVD bietet zahllose Möglichkeiten, da beinahe jedes Material abgeschieden werden kann: von reinen Metallen bis hin zu Legierungen, von Nitriden über Carbide bis hin zu Oxiden sowie Glas und Keramik. Darüber hinaus können die zu beschichtenden Gegenstände auch aus Metallen, Legierungen, Kunststoffen und Glas bestehen, was die Anwendungsgebiete dieser Technologie deutlich erweitert.
Metallisierung oder die Abscheidung einer dünnen Schicht aus metallischem Material wird häufig zum Schutz, zur Abschirmung oder zur Erhöhung der Reflektivität verwendet, grundlegende Eigenschaften von optischen Gegenständen wie Spiegel zur Bündelung und Umleitung von Lichtsignalen, Autoscheinwerfer oder in der Elektronik. Dieses Verfahren ist auch auf Kunststoffe und Glas, also leicht formbare Materialien, anwendbar, um die Vorteile einer Metalloberfläche mit Gegenständen mit komplexen Formen zu vereinen. Dies erklärt die Verbreitung der PVD-Verchromung in Bereichen wie der Automobilindustrie, für Griffe und Innenräume, in der Kosmetik, für Deckel und Behälter, an Möbeln, für Armaturen und Werkzeuge, aber auch in der Mode, für Accessoires wie Schnallen, Haken und Knöpfe sowie für Schmuck. In diesen Fällen ist es nicht ungewöhnlich, PVD- und PECVD-Technologien auch zum Hinzufügen einer zusätzlichen dünnen Glasschutzschicht einzusetzen, um die Korrosions- und Kratzfestigkeit zu verbessern.
Bestehend aus einem Materialstrahl in Richtung des zu beschichtenden Gegenstandes muss seine Form einige Anforderungen erfüllen. Tatsächlich kann PVD sehr tiefe und schmale Löcher nicht abdecken oder perfekte Gleichmäßigkeit in Innenbereichen oder schwer zugänglichen Bereichen garantieren. Um dieses Problem zu beseitigen, werden die zu beschichtenden Gegenstände üblicherweise an Stäben befestigt und mechanisch um mehrere Achsen gedreht, damit immer unterschiedliche Bereiche die Materialquellen passieren.
PVD wird häufig beim Fräsen und für Schnittelemente verwendet, da Beschichtungen auf Nitrid- und Carbonitridbasis leicht auszuführen sind. Sie zeichnen sich durch extreme Härte und hohe Haftung oder Eigenschaften aus, die die Effizienz verbessern und die Lebensdauer dieser mechanischen Komponenten verlängern. Dank der Möglichkeit, Verbundwerkstoffe herzustellen, können auch Farben wie Gold und Silber erstellt werden, ohne auf die Verwendung der jeweiligen Edelmetalle zurückzugreifen. Aber auch neue Farbtöne und Reflexionen, die aktuelle Trends am besten widerspiegeln, können entwickelt werden. Im dekorativen Bereich sind Strohgelb, Roségold, Schwarz oder Braun neue Farben, die Eleganz und Innovation mit dem Charme und dem haptischen Gefühl verbinden, das nur Metall bieten kann, wobei sein Glanz und seine Kratz- und Abriebfestigkeit aufrecht bleiben. Die Vielseitigkeit und Qualität von PVD-Beschichtungen gehören sicherlich zu den Stärken dieser Art von Anwendung.
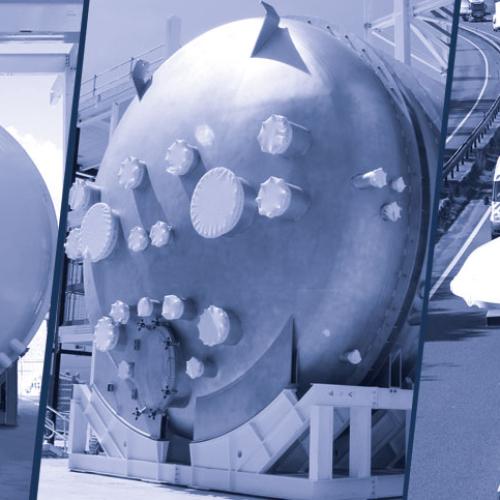
Die Installation eines der größten Raumsimulatoren Europas für das Rutherford Appleton Laboratory (RAL) in Großbritannien wurde in diesen Tagen abgeschlossen.